"관리란 무엇인가" 너무도 많이 들어오는 얘기다. 게다가 품질 관리라고 하는 얘기는 상투적이라고 할 만큼 흔한 얘기임이 분명하다. 하지만 문제는 이러한 질문을 했을 ? 이를 명확하게 답할 수 있는 우리 관리자가 별로 없다라고 하는 게 또 우리의 수준임이 분명한 것 같다. 관리의 의미를 정확하게 알고 그의 중요성을 인식하고 실천해나가는 것이 현재 우리 자동차 부품회사들이 만들어 가야 할 가장 시급하면 서도 중요한 숙제가 아닌가 생각한다.
|
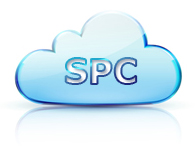 |
일본 자동차 회사의 경쟁력은 어디에서 오는가 라고 하는 재밌는 얘기를 들은적이 있다. 그 얘기의 결론은 일본이 세계에서 가장 관리를 잘하는 사람들이고, 실제 제조의 현장에서 그게 실현되어지고 있다는 것이다. "우리 제조현장에서 작업표준이 유효하게 사용되어지고 있는가"라는 아주 퀘퀘먹은 너무도 상식적인 기본마저도 의심스러운 경우가 솔직히 우리 주위에 너무도 많다. 얼마전에 내가 잘아는 지인이 작업표준의 준수성에 대해 평가를 해보았단다. 하는 방법은 작업표준의 내용을 아무도 모르게 바꾸어서 현장에 걸어놓고 어떤 반응이 오는지 기다리는 것이었다. 전날 밤에 바꾸었는데 하루종일 아무른 반응이 없었다고 한다. 근데 퇴근 시점에 여자 반장이 작업표준서를 가지고 와서 하는 얘기는"사장님 작업표준이 잘못되어 있습니다, 그래도 우리는 제대로 일을 했으니 걱정하지 마세요" 너무도 훌륭한 우리의 감독자 들이다?
그래도 이정도 수준이면 그렇지 않은가, 확인도 하지 않는 관리자가 대부분인데.
관리(협의)란 조치를 위한 한계를 정해서 한계를 벗어나는 지를 모니터링하고 문제가 있으면 조치토록 하는 것이라고 했다. 집사람이 하는 얘기가"애들을 공부시킬려면 관리를 잘해야 한다고 한다"라고 하기에 관리가 무엇인지 물었더니, 그건 모르겠는데 하여튼 관리를 잘 해야 한다는 얘기다. 그렇다 자세한 정의는 잘모르겠지만 하도 많이 들었던 것이라 인지상정으로 다 알고 있다고 할 수 있겠다.
그럼 우리 제조 현장에는 어떻게 적용할 것인가.
분명하다 PDCA로 하는 것이다.
1. P: 관리기준을 정하고(몸무게를 60Kg으로 관리해야 하겠다.)
매일 밥은 어느정도 먹고, 운동은 어떻게 하고
2. D: 실행하고
3. C: 몸무게를 체크하고
4. A: 60Kg가 넘으면 무엇이 잘못되었는지 조사 해서 조치하고
아주 간단한 문제이다.
근데 제조 현장도 몸무게 처럼 변화의 산포가 아주 천천히 움직여준다면 얼마나 좋을까.
불행하게도 그러하지 못한게 제조현장의 공정이라고 하겠다. 공정을 구성하고 있는 4M은 우리도 모르는 사이에 항상 변하고 있으니. 기준은 세웠으나 변화했는지 하지 않았는지를 체크해 내는 능력이 너무도 중요한 것같다. 그렇다고 제품이 나올 때마다 매시간 측정한다는 것도 비용의 문제 때문에 어려운 것같고, 어떻게 할 것인가?
예를 들어 도장공정의 도막의 두께라고 해보자.
측정을 해본다면 우리가 얘기하는 산포라고 하는 형태로 도막의 두께가 형성되고 있음을 쉽게 알 수 있을 것이다. 그것도 매번 측정시마다 DATA를 달리 하면서 말이다. 문제는 여기서 부터 출발한다. 분명히 도장 공정에 몇가지 중요한 관리점과 관리기준을 가지고 있을 것이다. 측정값이 변했는데 그럼 그 관리점들이 유의하게 변동했다는 것인가 하는 점이다.
품질을 만드는 방법은 무엇인가, 우리가 관리하고 했던 관리점들이 변화하지 않고 그대로 준수되어진다면 분명 그 측정의 DATA도 일정하게 유지 될 것이다. 하지만 이것은 이론 일 뿐이다, 아마 실헙실에서 제조를 한다면 이 말이 통용될 수 있을 지도 모르겠다. 제조 현장은 불행이도 우리가 관리 할려고 하는 관리점이 외에 또다른 많은 요인에 의해 분명 변화되어지고 있을 것이다. 이러한 상황 속에서 우리는 어떻게 우리가 관리하고 자 했던 요소들이 변동하고 있는지를 발견해내고 조치하고 할 수 있을 것인가?
이렇게 하는 것을 관리라고 했는데, 그리고 지난번 얘기에서 이런 요소들의 변동을 이상원인이라고도 했는데, 이상원인!! 이게 문제다.
출근 준비 때문에 나중에 다시.